The 32 sq ft conundrum
How to minimise laminate wastage while making wardrobes
Minimising material wastage during the lamination of wardrobes requires a combination of careful planning, precise measurements, and efficient utilisation of laminates. Here's a technical guide to help reduce material wastage in the lamination process:
1. Accurate Measurements and Planning:
Begin by obtaining accurate measurements of the wardrobe components. Detailed measurements help optimise the layout of laminates and minimise the need for excessive trimming. Plan the lamination process meticulously, considering each panel's dimensions and the overall design.
2. Computer-Aided Design (CAD) Software:
Utilise CAD software to create detailed wardrobe design drawings. CAD allows for precise visualisation and planning, helping to optimise the placement of laminate sheets on each wardrobe component. It also enables you to create cutting patterns that minimise wastage.
3. Optimised Cutting Patterns:
Use the CAD software to generate optimised cutting patterns for laminates. Arrange the pieces on laminate sheets in a way that minimises offcuts. This includes employing nested cutting techniques to fit components together efficiently and reduce unused areas on the laminate sheets.
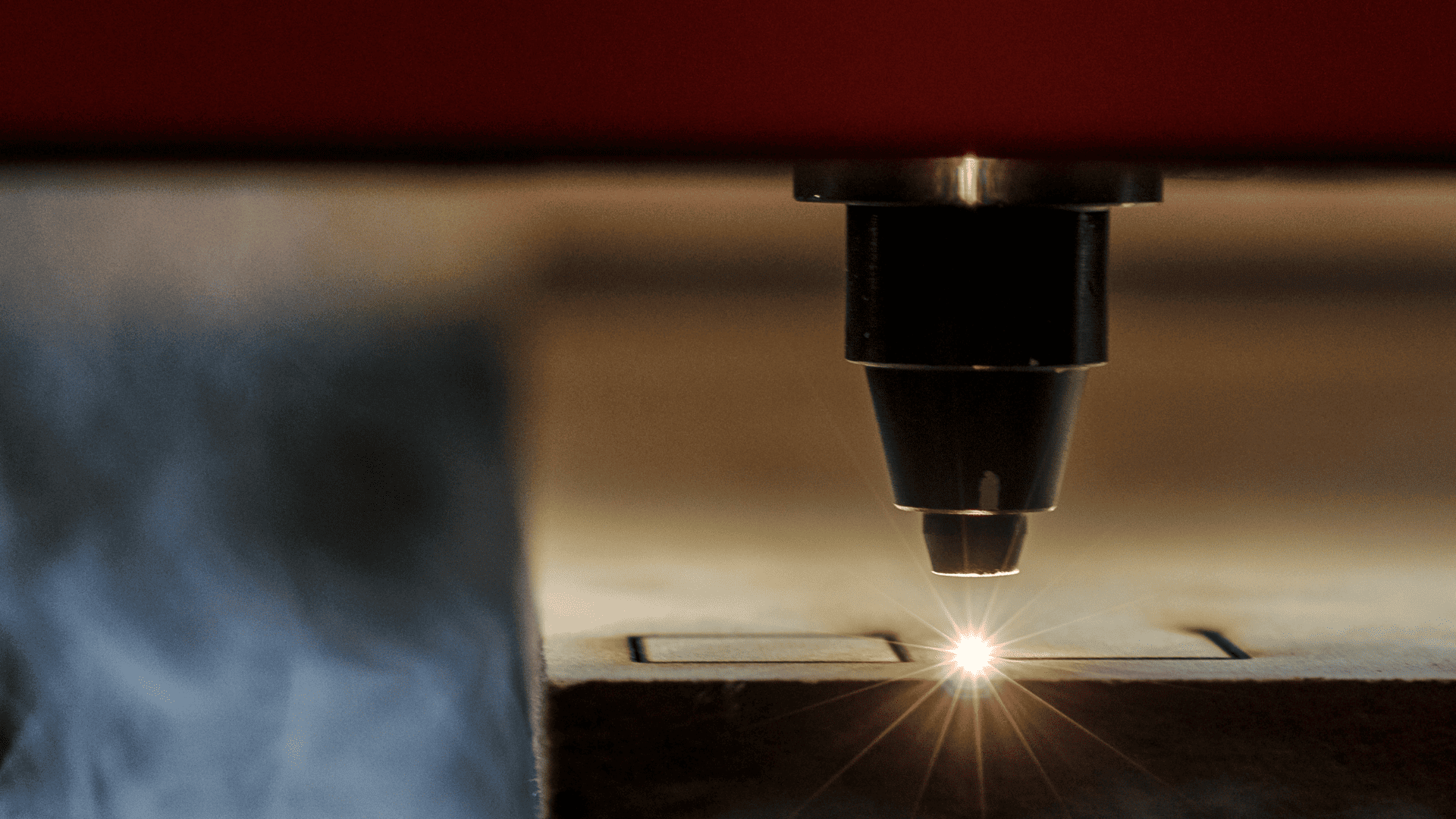
4. Standardised Panel Sizes:
Standardise panel sizes wherever possible to reduce the need for custom-sized laminates. Yes, most cupboard depths are 24”, but can the widths also be designed to be a multiple of the width of the laminate? Standard sizes minimise wastage during the cutting process, as larger, unaltered sheets can be used for multiple wardrobe components.
5. Precision Cutting Equipment:
Invest in precision cutting equipment for laminating processes, such as CNC machines. These machines offer accuracy and efficiency, reducing the likelihood of errors resulting in wastage. CNC machines can follow the optimised cutting patterns generated by CAD software.
6. Material Selection:
Carefully select laminate sheets based on their dimensions and suitability for the wardrobe design. Choosing laminate sheets that closely match the required panel sizes helps minimise cutting waste. Consider using roll laminates for continuous surfaces to reduce seams and wastage further.
7. Consider Grain Direction:
Pay attention to the grain direction of laminates, especially if they have a wood grain pattern. Aligning the grains strategically across panels ensures a cohesive look while minimising the need for excess trimming.
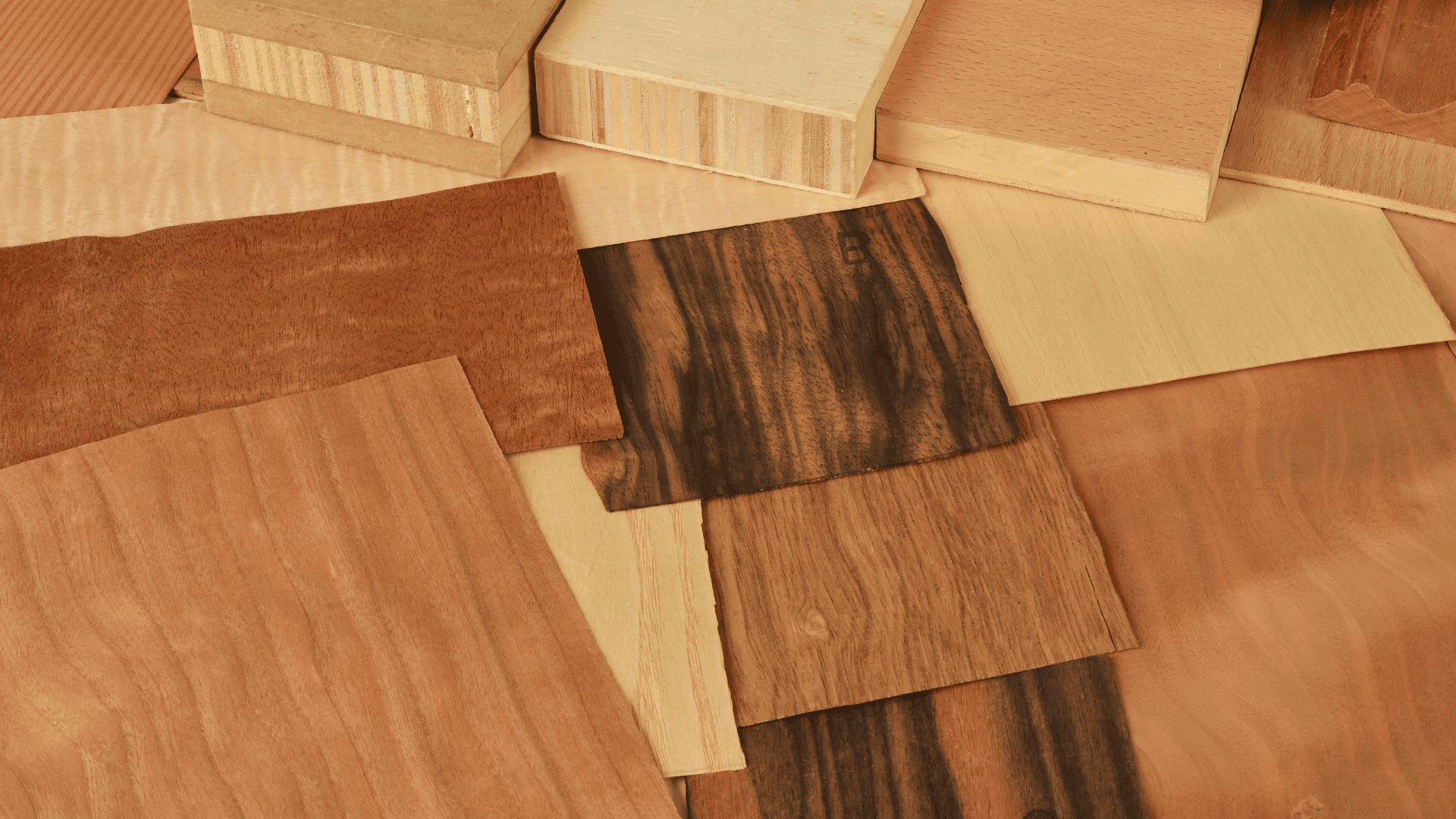
8. Utilise Offcuts:
Plan for the use of offcuts in areas where smaller laminate pieces are needed. Offcuts can be repurposed for smaller components or used as edge banding, reducing overall material wastage.
9. Quality Control Measures:
Implement stringent quality control measures during the lamination process to minimise errors that could lead to wastage. Regularly check laminate placement, adherence, and cutting accuracy to ensure optimal material utilisation.
10. Contractor Training:
Train workers involved in the lamination process to handle materials efficiently and accurately operate cutting equipment. Proper training reduces the likelihood of errors and ensures the laminating process is carried out with minimal waste.
By incorporating these technical strategies into the lamination process for wardrobes, manufacturers can significantly minimise material wastage, optimise laminate utilisation, and enhance overall efficiency in production.